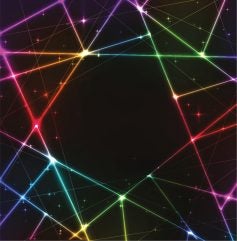
Suburban New Jersey is perhaps not where you’d expect an engineering revolution to start. Yet it was here, in 1965, that technicians at the Western Electric Engineering Research Center first developed a machine that used lasers to drill holes in diamond dies. By the 1970s, the technology was regularly used in specialised sectors like aircraft manufacturing – and by the following decade represented a clean, accurate and effective alternative to traditional joining. Given, moreover, the bewildering range and complexity of medical devices, it didn’t take long for lasers to dominate pharma manufacturing too. That’s obvious enough from the numbers: according to work by Research and Markets, the global laser processing market is currently worth over $18bn, a figure expected to reach $26bn by 2027 – this growth is largely down to surging interest in lasers across the medical devices sector.
Yet if they’re now a common sight across medical production lines, everywhere from cutting and welding to drilling and marking, not every laser is created equal. Especially with the increasing proliferation of ultra-intricate machines, often optical in nature, traditional manufacturing lasers can struggle, particularly when it comes to damaging the device. Yet the situation is far from hopeless. For amid the proliferation of nanosecond devices, so named for the laser pulses they emit, a newer range of femtosecond lasers are appearing too. Boasting much faster pulses than their nanosecond cousins, they can focus energy to remarkably precise points, ensuring hollows are dug or seams welded without harming surrounding material.
Not that manufacturers can necessarily expect to seamlessly convert to femtosecond solutions. As so often, reliability is one difficulty. Price, for its part, is another. And while both these stumbling blocks are gradually being softened thanks to widening adoption, and the market forces that implies, researchers are tackling problems around low manufacturing throughput via the clever use of technology. Not that every manufacturing challenge should necessarily be solved by femtosecond lasers. For while their value is indisputable, particularly for manufacturing sophisticated devices like cardiovascular stents, other products may actually be produced better using older lasers – especially if cost is an issue.
Cutting crews
It’s hard to overstate the importance of lasers across medical device manufacturing. Consider something as straightforward as welding. Excellent at combining metallic materials, they’re crucial for the manufacture of pacemakers and stents. That’s true in other areas too. As Professor Robert Thomson, a photonics expert at Heriot-Watt University highlights, lasers can equally be employed for drilling holes in needles and catheters, or else marking (engraving) implants and surgical tools. That’s echoed, adds Duncan Hand, another Heriot-Watt professor and laser expert, by 3D printing, where lasers can be used to print complex electrical structures onto living organisms.
Quite beyond the headline industry growth, meanwhile, this enthusiasm is apparent if you examine specific firms. Stryker, for instance, has been investing in laser manufacturing capabilities for years, while Medtronic has recently focused on using lasers to enhance the surface textures of devices. Listen to the experts, and this popularity can fundamentally be understood in terms of how lasers works. Targeting pulses, and the energy they emit, to very specific areas, they can cut holes or dig groves – all without damaging nearby material.
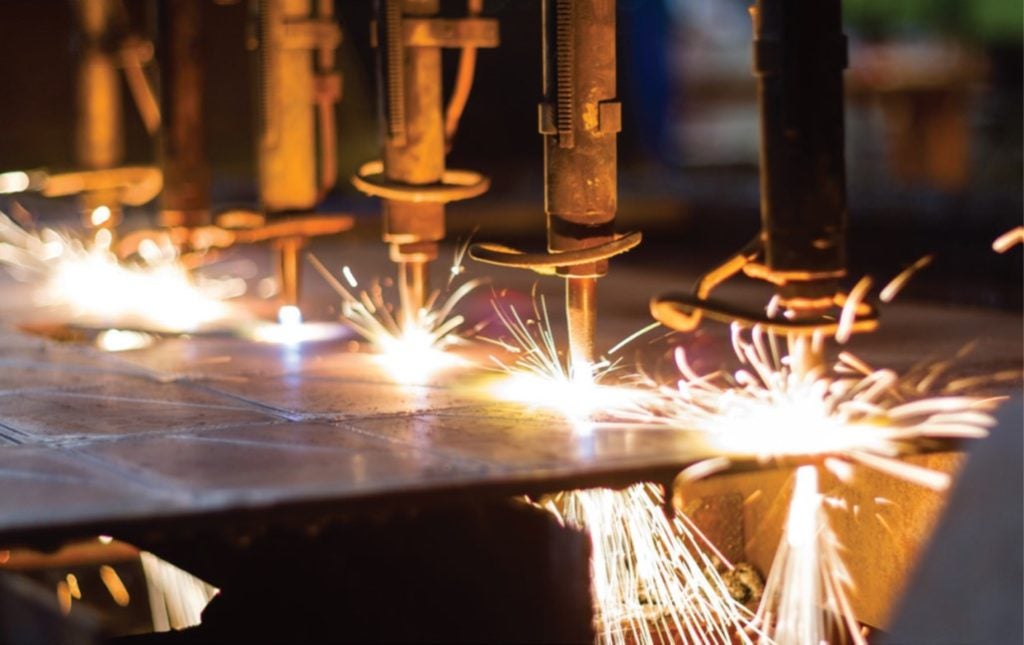
Beyond the benefits for intricate and fragile medical components, that’s equally helpful for manufacturers wishing to create lattice structures from materials. Among other things, these lattices can mimic bone (stimulating ingrowth) and change the mechanical behaviour of existing materials (reducing the need for complex polymers). As Thomson summarises: “In comparison to conventional manufacturing approaches, such as mechanical drilling, lasers offer the potential for micron-level precision, they are more flexible in terms of the range of materials to which then can be applied, they can provide a cleaner, more repeatable, and potentially more environmentally friendly manufacturing process, and they do not exhibit tool wear.”
“Lasers offer the potential for micron-level precision…and they do not exhibit tool wear.”
Robert Thomson
Despite these general advantages, however, the properties of some lasers can also cause frustration. As Dr Koji Sugioka of the Riken Center for Advanced Photonics explains, that’s basically down to speed. “The important factor for materials processing using lasers,” he says, “is the electron-phonon coupling time of materials – which is the time during which the laser energy absorbed by electrons is transferred.” The problem, continues Sugioka, is when the pulse width of a particular laser is longer than the electron-phonon coupling time. That can spread the laser heat to other areas, along the way causing severe damage. Of course, this can be disastrous, both technically and financially, especially now that miniaturisation is the order of the day right across medical device manufacturing.
$26bn
The expected size of the global laser processing market by 2027.
Research and Markets
Laser focus
Given the limitations of longer pulse lasers – notably the nanosecond variety – it makes sense that researchers should have focused many of their efforts on short-pulse alternatives.
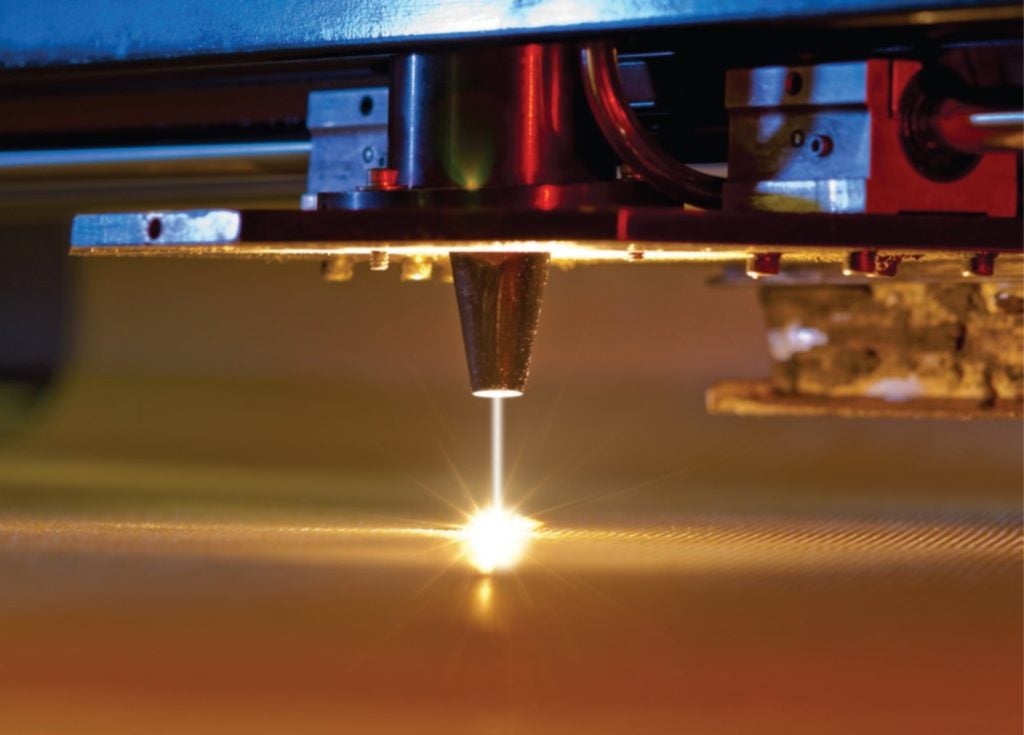
The most popular example here involves so-called femtosecond lasers. Emitting pulses lasting just a millionth of a billionth of a second, in Thomson’s telling they “maximise the efficiency” with which the electrons in a material are stimulated. Hand makes a similar point. As he explains, the peak power of femtosecond devices is “so high” that pulses can be sent through a material – without damaging it. That means, he adds, that manufacturers “can actually machine inside things” without impacting the external structure.
“The performance of femtoseconds is growing year by year and the price is decreasing.”
Koji Sugioka
As Hand implies, the practical benefits of this technology are unsurprisingly vast. Perhaps most important is the remarkable focus of femtosecond lasers, with Thomson stressing that the “efficiency of laser manufacturing processes such as drilling and cutting can be maximised” without damaging nearby material. And if that’s useful right across the sector, Sugioka is keen to highlight the particular value of femtosecond machines in crafting high-tech medical solutions. One example are so-called ‘lab-on-a-chip’ devices, which integrate sophisticated DNA sequencing or biochemical detection capabilities into a tiny collection of wires and circuit boards. And if that obviously has eye-catching medical consequences – potentially allowing us to diagnose cancer and Alzheimer’s, among other conditions – Sugioka says that labs-on-a-chip represent “one of the most relevant applications” of femtosecond lasers.
That’s shadowed, Sugioka notes, by the fabrication of ‘nano’ devices. One example are microvalves that prevent the reversal of blood flow in human veins; another are microneedles for transdermal drug delivery. For their part, both Thomson and Hand emphasise the potential of femtosecond lasers to assist in the building of optical components. Offering an example, Thomson describes his work on what’s known as Raman spectroscopy, an analytical technique to understand chemical structures. “The micro-optic systems we have developed,” he says of his team’s new biopsy devices, “not only enable the Raman to pump light to be focused into the tissue, and the Ramanshifted light to be efficiently collected, they also provide passive alignment features for optical fibres.” Ultimately, Thomson adds, this could lead to the development of probes that don’t require the alignment of fibres and optics. That could cut costs drastically – something that wouldn’t have been possible without ultrafast laser inscription (ULI).
Mix and match
To put it differently, femtosecond lasers and similar machines promise to revolutionise medical practice. All the same, it’d be wrong to imagine that these devices are a panacea. For one thing, several experts highlight the price of ultrafast pulse lasers. Fair enough: according to one estimate, they can cost manufacturers as much as $250,000. Sugioka has broader concerns, arguing that “increasing laser power, and the reliability of laser systems, is definitely necessary”. Then there’s the question of whether femtosecond machines are even always needed. After all, though Hand is excited about the potential of femtosecond solutions, he stresses that older models shouldn’t be consigned to the scrapheap. As he puts it: “If they’re suitable for your process, the longer pulse lasers are lower cost, so they’re better to use.”
Yet if less complicated devices, for instance pacemaker containers, can be comfortably welded using nanosecond lasers, there are signs that change is coming to the femtoseconds too. “The performance of femtoseconds is growing year by year,” Sugioka says, “and the price is decreasing thanks to the great effort of laser manufacturers. Therefore, I’m very optimistic about the use of femtosecond lasers on production lines in the near future.” Thomson, for his part, is similarly sanguine. Especially when it comes to stents and other essential kit, he says that femtosecond technology has already proved transformative. And though he’s uncertain about its application in other areas, he suggests the potential of ULI is “too attractive a capability” for manufacturers to ignore. If only those early innovators in New Jersey could come back and see it.